W
WSnyder
Guest
I could never figger out why they wouldn't have them at dead nuts 90's.
With 3 pinions, 3 attachment bolts for the backplate and 4 adjustment screws there doesn't appear to be enough room. I'd like to take one of the older Buck's w/the 90° spacing apart and see how they did it. Maybe the older Buck's have only 1 pinion in them. I believe Jackie Schmidt has an older Buck w/the 90° adjustments. Maybe he could answer the question.
Edit: I looked at some pictures of the older Buck set-tru's. They appear to have only one pinion for jaw opening/closing. Probably why they had room for 90° adjustment screws. Some of the newer Bison and Buck set-tru's have 3 pinions in them although the latest Buck's appear to have gone back to one pinion and 90° adjustments. Bison still seems to have the 3 pinion and non 90° adjustment design.
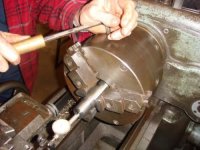
Last edited by a moderator: