J
josh82
Guest
Custom build based on a Ruger American action.
Al started out, because I was looking for a cheap bolt action gun for foxing in 223. Finaly I settled on a Ruger American compact stainless, in 223. As the box came in, I started directly with making some quality ammo for that thing. Had already some Lapua 223 cases ready, and loaded them up with Sierra Match Kings, 69 grain BTHP, went to the range, and shot it a bit, I was shocked, no group under 2 inches…
Made my way home totally disappointed, and thinking what to do, I could send it back… as I came home I packed that thing away and, tried to forget about the bad day.
But I wanted to make anyway a custom gun some time, I started thinking about taking this receiver as a basis for my project. I pulled the barrel, and totally disassembled the gun. Just with the bolt and the receiver I went to my company as I have all the dedicated measuring equipment which my home shop lacks. I just wanted to make sure that the receiver is fairly straight to start with. And to my surprise it was totally straight, even with a multi thousand dollar 3d measuring machine it proved to be straight. Then I measured concentricity off the bolt hole, and that was fine too, but the internal finish was horrible, they just bored that hole with a dull boring bar, the surface, I would have made better with a hacksaw… ok here we go…
Ordered a Lothar Walther SS barrel, and as I wanted to lap it myself I ordered it without match finish and, I’ve chosen thr bore and groove diameter to be 5 tenthou under actual measured bullet diameter. Sent them an email and waited for their reply, they said that barrel would be out of CIP/SAAMI spec, and I said, here in Switzerland we don’t care about that. And they agreed to send me a pressure test barrel which meet my spec.
Once the barrel was in I made myself a lapping jig, and started lapping the barrel, until it matched my bullet diameter of my SMK69 grainers. As I lapped the barrel I kept slugging and measuring, and as I reached final diameter just a hair under my actual bullet diameter, I stoped lapping, to save some 1-2 tenthou for the final finish.
Moved the barrel over to my CNC lathe and dialed in the bore, until I couldn’t measure any runout with my 1 thenthou dialindicator.
My loaded round measures .252 so I went for a .250 neck diameter. As I didn’t had a reamer handy I went to my company and stuck a piece of HSS rod in a CNC grinding machine, programmed the coordinates and pressed the start button and went for a coffe… after measuring my reamer, and making sure all dimensions where as I wanted, I went home again and started chambering my barrel. All went fine. Then I threaded the barrel tennon to 1” 16tpi, that went well, then I checked the fit with my receiver, it was a bit stiff so I decided to screw it off, and that ing thing won’t move anymore… It galled on there…. I should have known that, but as I work mostly with tool steel I just forget about putting some good anticease in there… good I cut the barrel off in front off the receiver and bored the plug out. Lesson learned!
I started all over and that time with antiseize all went well.
Then when all was finished I wanted to use the origanl stock for the function test, and I hacksawed the sides off the forend away to make room for that fat barrel, but it was so flexy that I screwed that piece off plastic off and threw it in the bin, where such a cheap stock belongs.
I had a salvaged target stock in my basement, from a target airrifle, then I tried to fit that, but the stock wouldn’t fit in any way I would cut and file it…
So as time is a little bit off concern, I decided to just buy something I can just screw on. As here in Europe the aftermarket support is quite small for American made rifles. I went for the only option which was stiff and had good bedding right away. The MDT LSS chassis. Which proved to be a good decision.
When that thing came in I bolted it all together, and headed to the range.
Wow, wow wow, no load work up nothing, it just grouped in the .3’s as you can imagine I am a happy camper.
Al started out, because I was looking for a cheap bolt action gun for foxing in 223. Finaly I settled on a Ruger American compact stainless, in 223. As the box came in, I started directly with making some quality ammo for that thing. Had already some Lapua 223 cases ready, and loaded them up with Sierra Match Kings, 69 grain BTHP, went to the range, and shot it a bit, I was shocked, no group under 2 inches…
Made my way home totally disappointed, and thinking what to do, I could send it back… as I came home I packed that thing away and, tried to forget about the bad day.
But I wanted to make anyway a custom gun some time, I started thinking about taking this receiver as a basis for my project. I pulled the barrel, and totally disassembled the gun. Just with the bolt and the receiver I went to my company as I have all the dedicated measuring equipment which my home shop lacks. I just wanted to make sure that the receiver is fairly straight to start with. And to my surprise it was totally straight, even with a multi thousand dollar 3d measuring machine it proved to be straight. Then I measured concentricity off the bolt hole, and that was fine too, but the internal finish was horrible, they just bored that hole with a dull boring bar, the surface, I would have made better with a hacksaw… ok here we go…
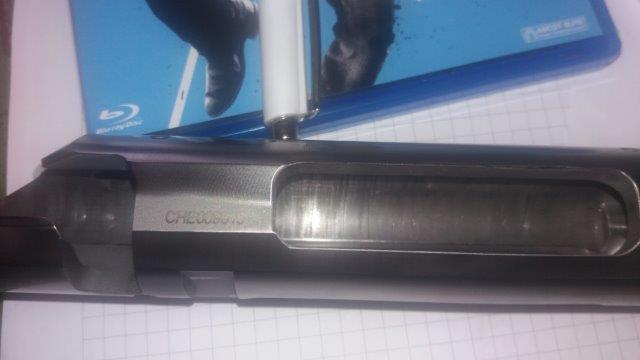
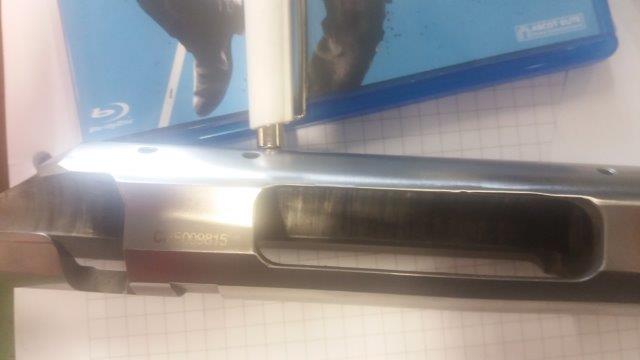
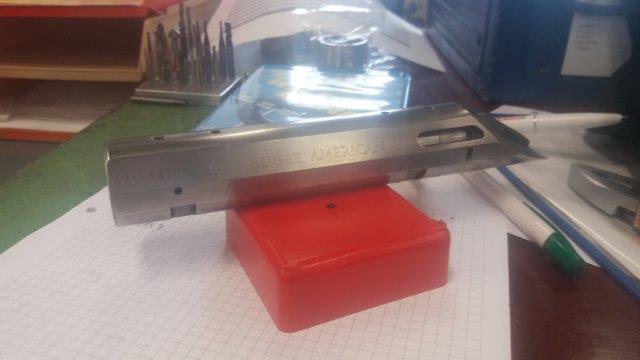
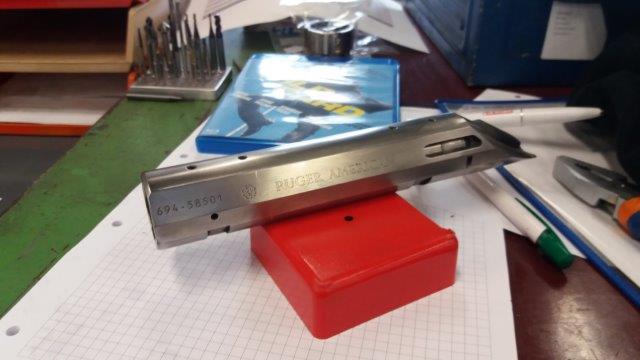
Ordered a Lothar Walther SS barrel, and as I wanted to lap it myself I ordered it without match finish and, I’ve chosen thr bore and groove diameter to be 5 tenthou under actual measured bullet diameter. Sent them an email and waited for their reply, they said that barrel would be out of CIP/SAAMI spec, and I said, here in Switzerland we don’t care about that. And they agreed to send me a pressure test barrel which meet my spec.
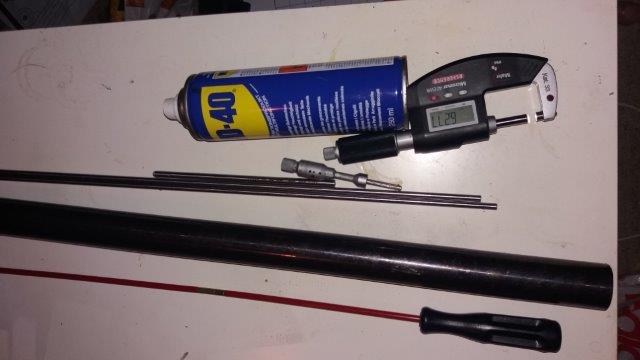
Once the barrel was in I made myself a lapping jig, and started lapping the barrel, until it matched my bullet diameter of my SMK69 grainers. As I lapped the barrel I kept slugging and measuring, and as I reached final diameter just a hair under my actual bullet diameter, I stoped lapping, to save some 1-2 tenthou for the final finish.
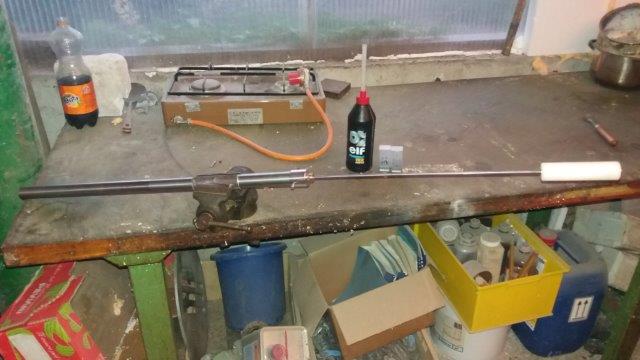
Moved the barrel over to my CNC lathe and dialed in the bore, until I couldn’t measure any runout with my 1 thenthou dialindicator.
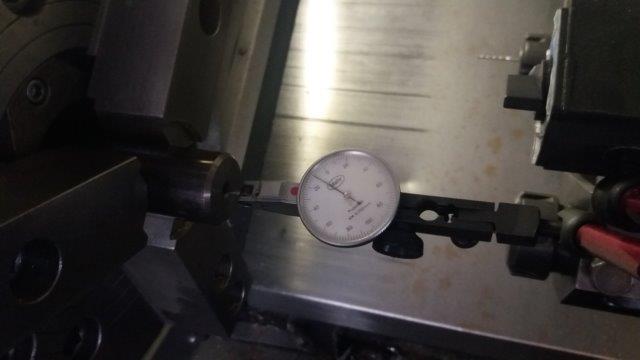
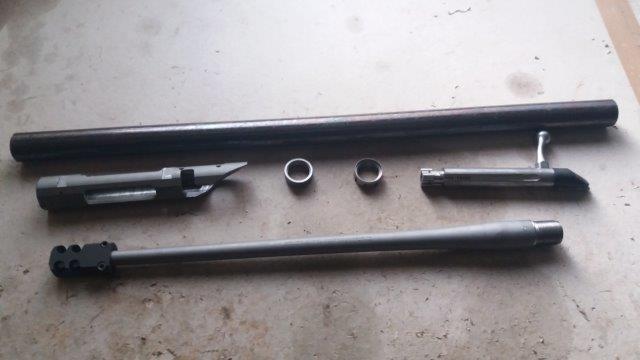
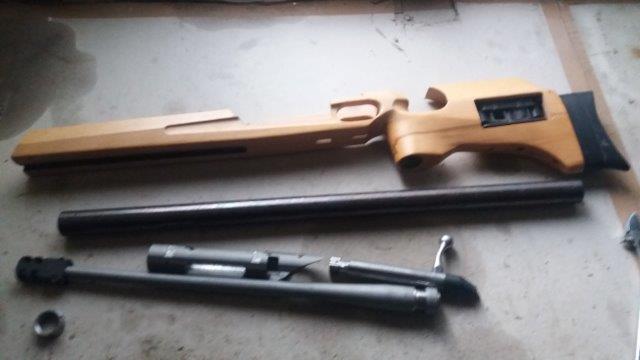
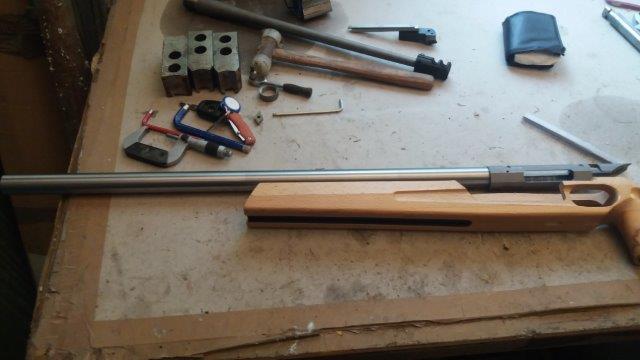
My loaded round measures .252 so I went for a .250 neck diameter. As I didn’t had a reamer handy I went to my company and stuck a piece of HSS rod in a CNC grinding machine, programmed the coordinates and pressed the start button and went for a coffe… after measuring my reamer, and making sure all dimensions where as I wanted, I went home again and started chambering my barrel. All went fine. Then I threaded the barrel tennon to 1” 16tpi, that went well, then I checked the fit with my receiver, it was a bit stiff so I decided to screw it off, and that ing thing won’t move anymore… It galled on there…. I should have known that, but as I work mostly with tool steel I just forget about putting some good anticease in there… good I cut the barrel off in front off the receiver and bored the plug out. Lesson learned!
I started all over and that time with antiseize all went well.
Then when all was finished I wanted to use the origanl stock for the function test, and I hacksawed the sides off the forend away to make room for that fat barrel, but it was so flexy that I screwed that piece off plastic off and threw it in the bin, where such a cheap stock belongs.
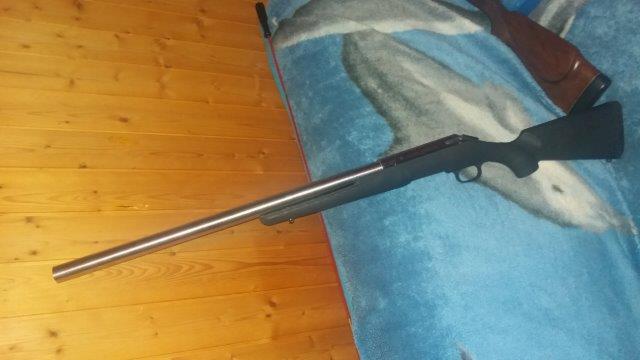
I had a salvaged target stock in my basement, from a target airrifle, then I tried to fit that, but the stock wouldn’t fit in any way I would cut and file it…
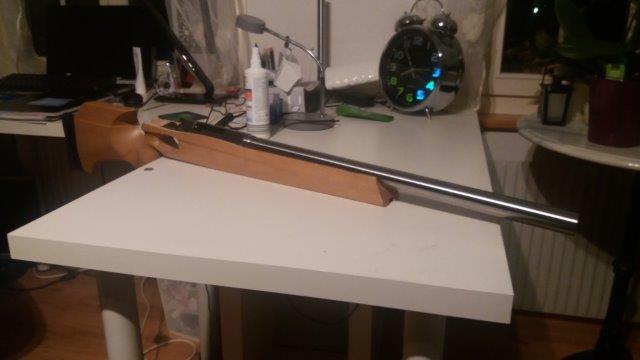
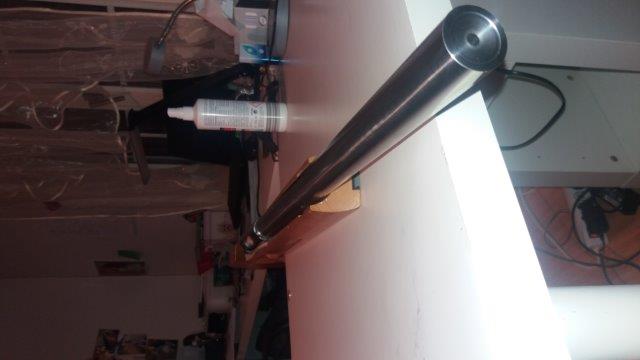
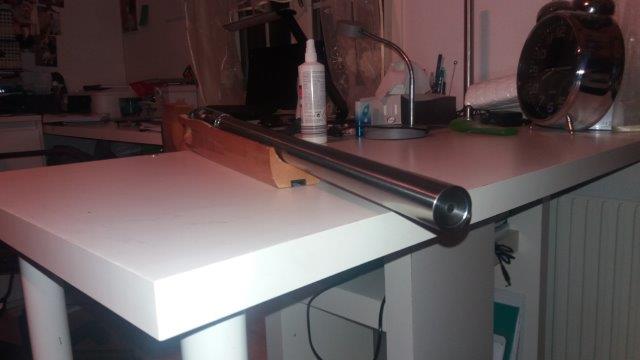
So as time is a little bit off concern, I decided to just buy something I can just screw on. As here in Europe the aftermarket support is quite small for American made rifles. I went for the only option which was stiff and had good bedding right away. The MDT LSS chassis. Which proved to be a good decision.
When that thing came in I bolted it all together, and headed to the range.
Wow, wow wow, no load work up nothing, it just grouped in the .3’s as you can imagine I am a happy camper.
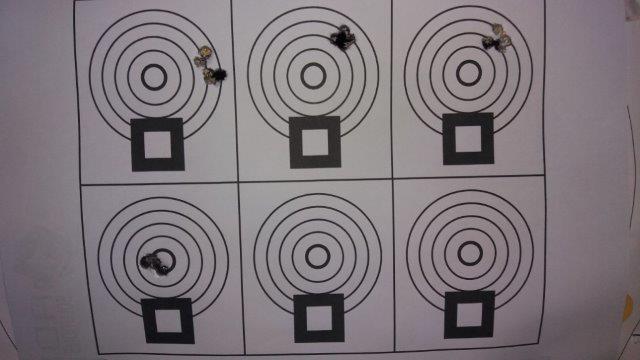
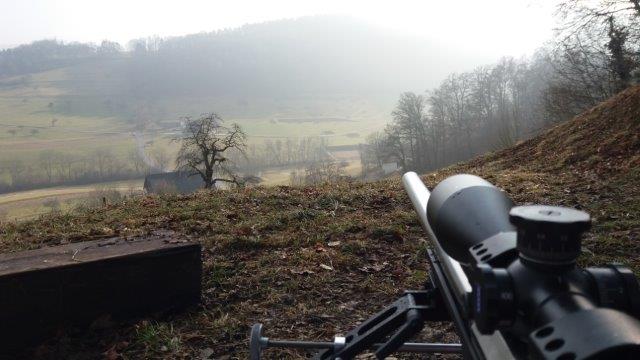
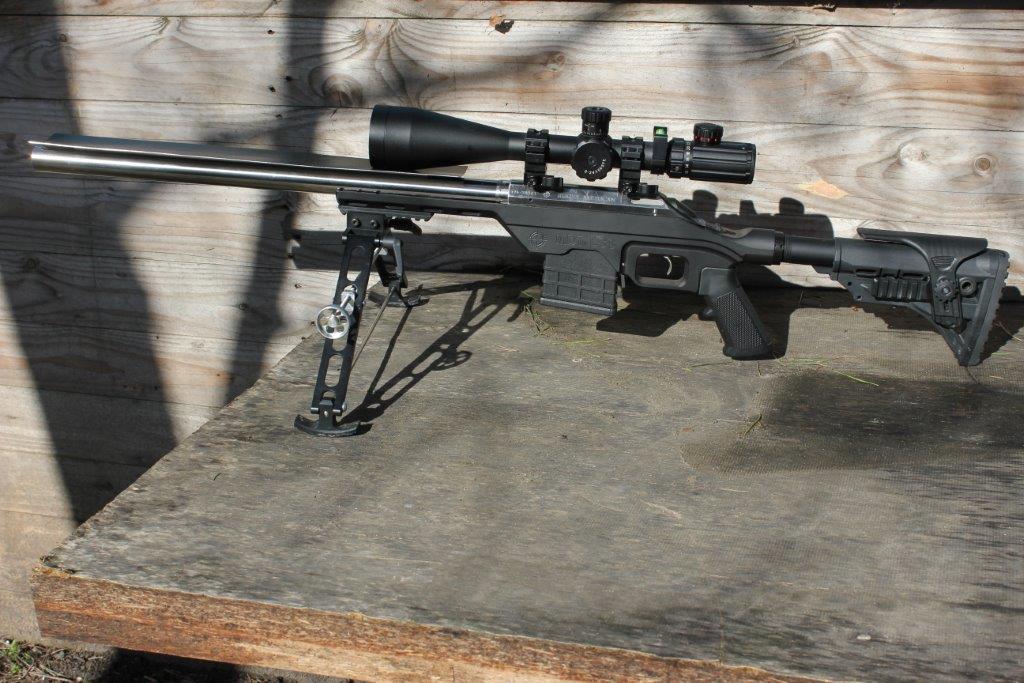
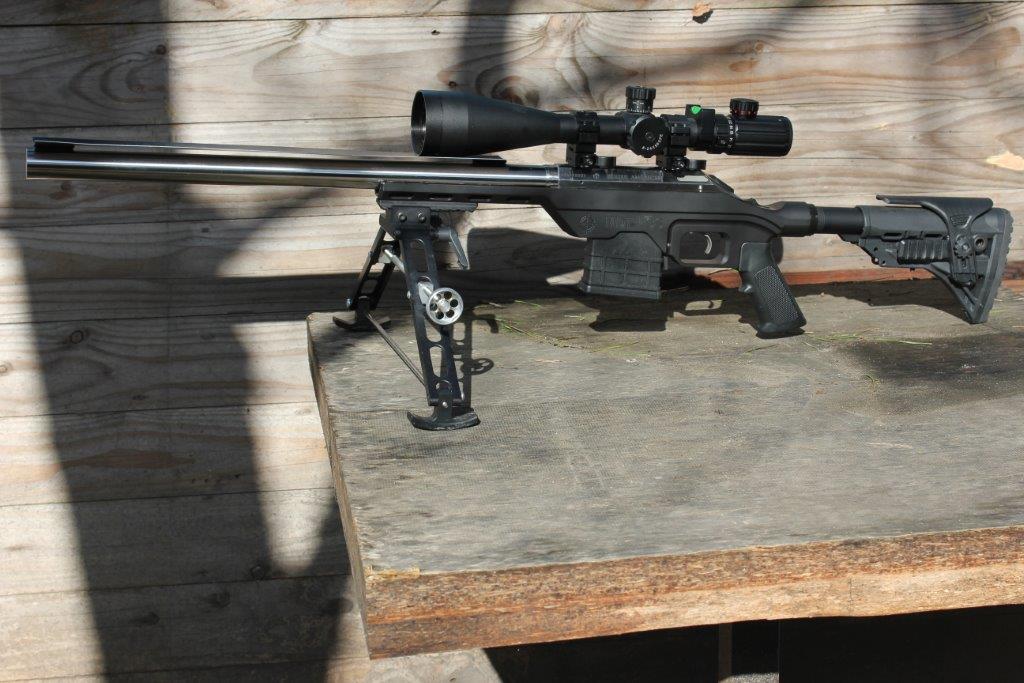
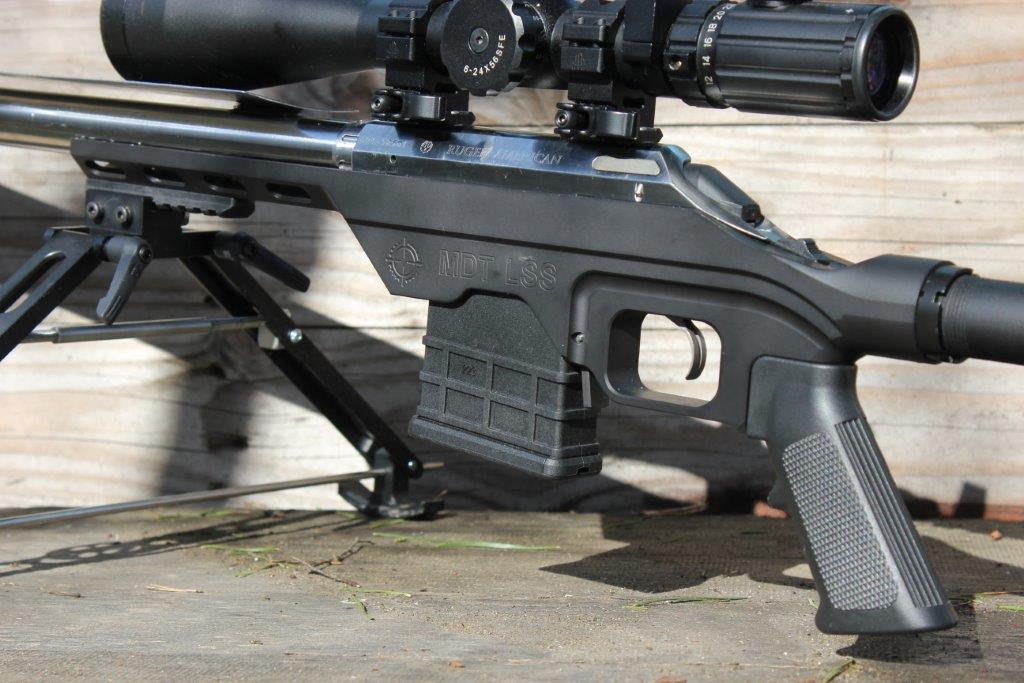
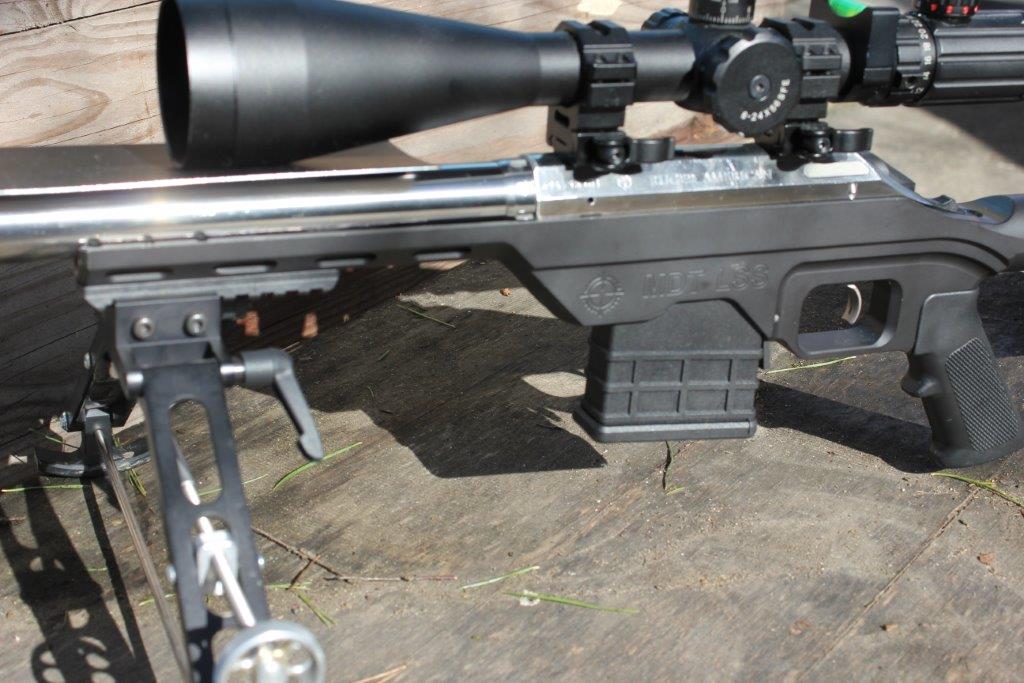
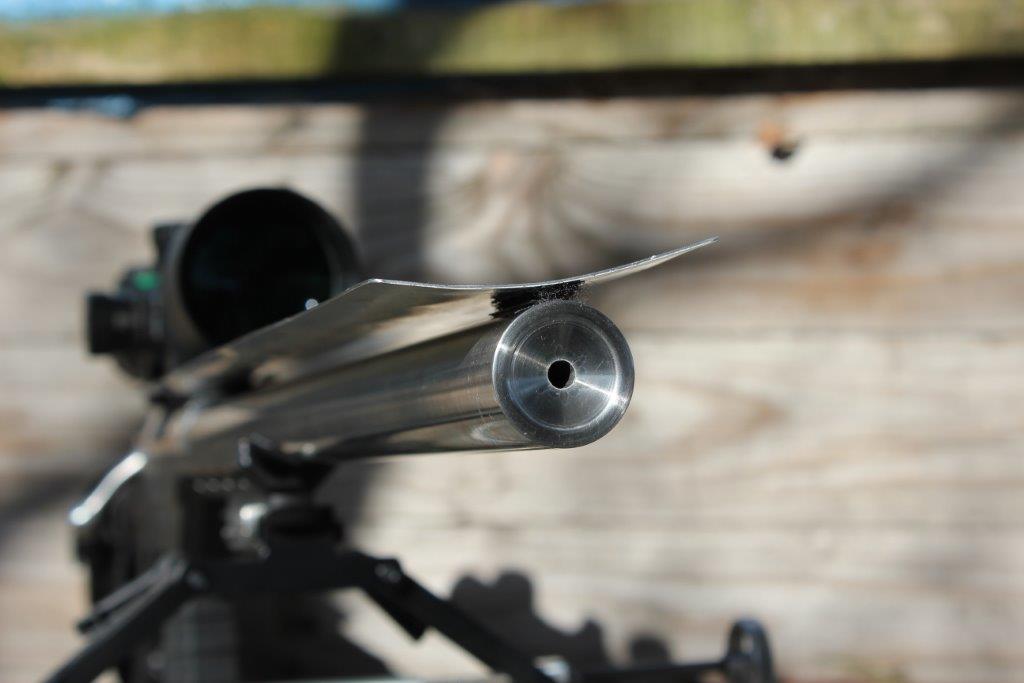
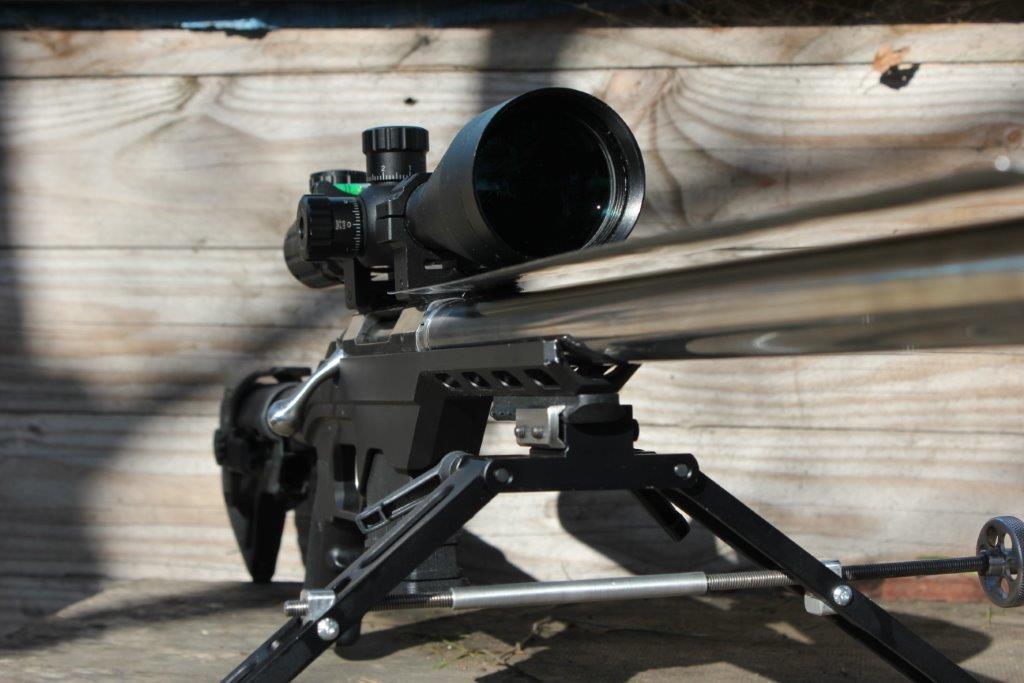
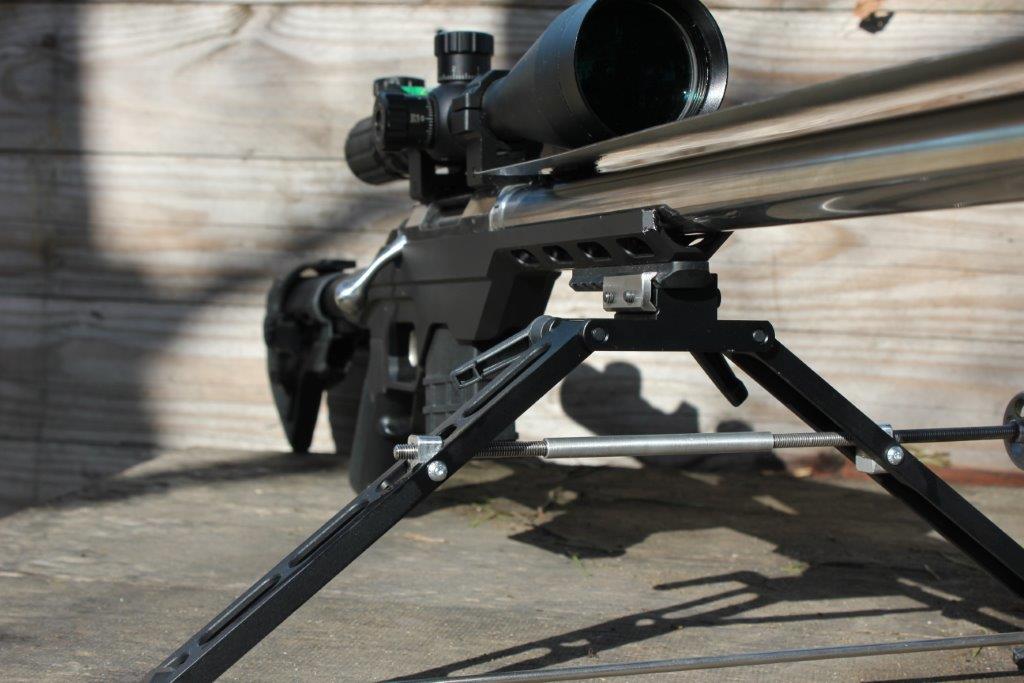
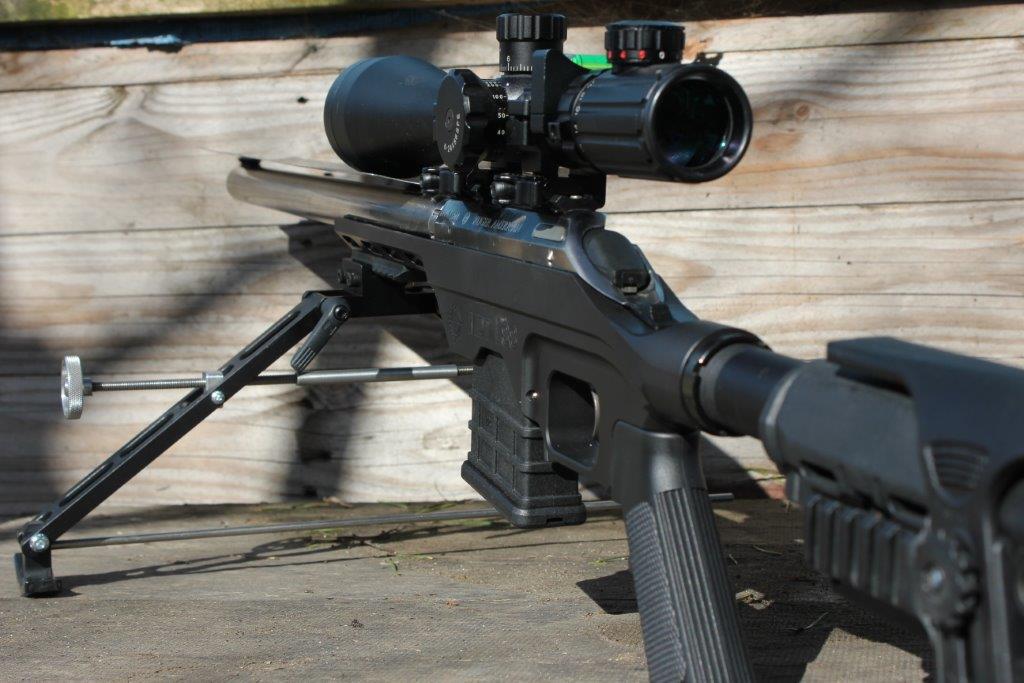
Last edited by a moderator: